Introduction
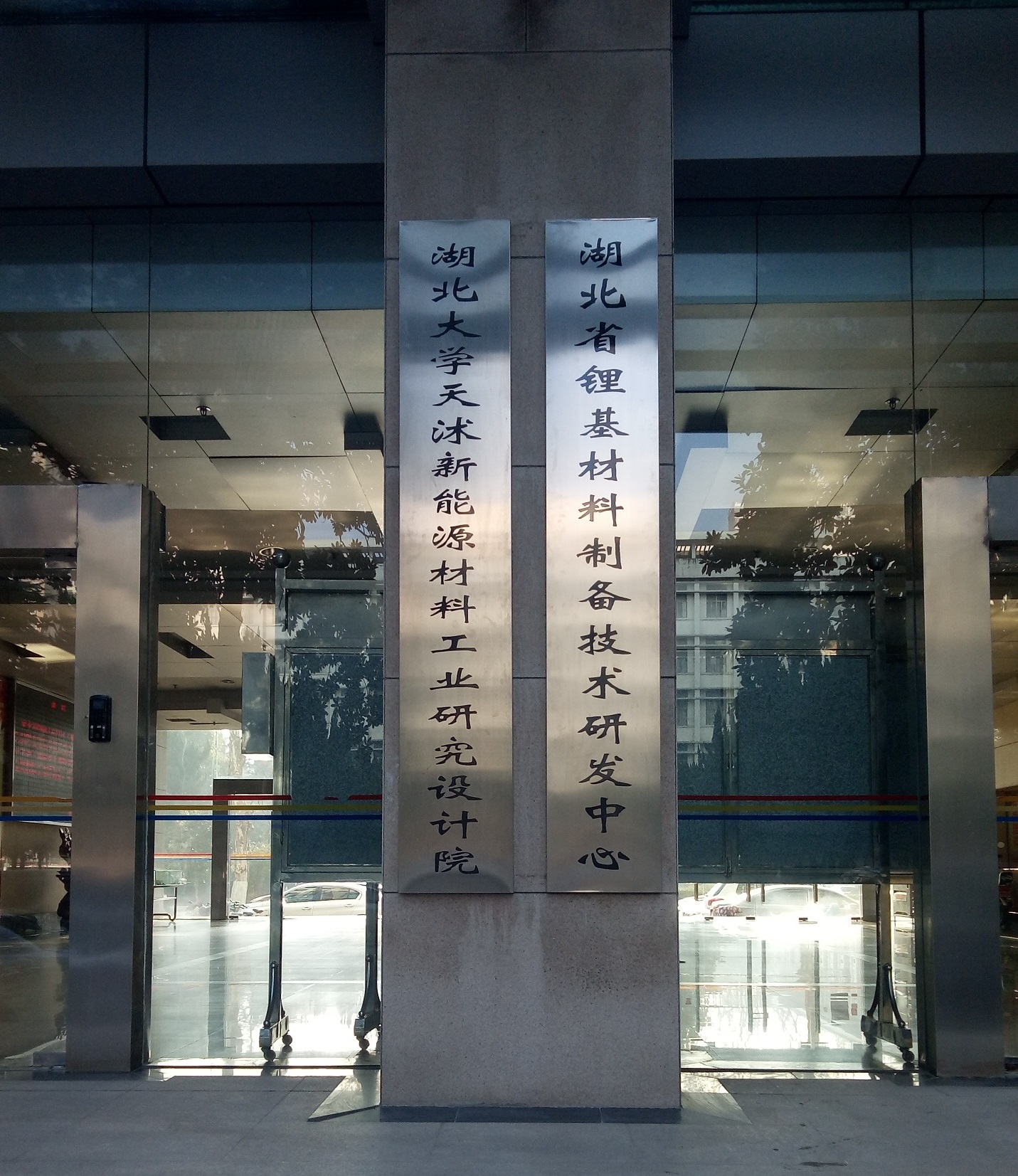
I.Preface
Hubei University Tianshu Industrial Research and Design Institute of New Energy Materials has the professional qualification of Grade B in Chemical, Petrochemical and Pharmaceutical Industry (Chemical Engineering). And our institute was recognized as “Hubei Provincial Research and Development Center of Lithium-based Materials Preparation Technology ” by Science and Technology Department of Hubei Province on December 27, 2017.
Lithium-based materials (lithium hydroxide, lithium carbonate, etc.) are the main raw materials for the production of metallic lithium and its isotopes and various fine lithium salts. They are widely used in lithium battery, cobalt and nickel extraction technology, chemical industry, metallurgy, medicine, aircraft, new energy vehicles, electronic information, nuclear power generation, non-metallic mineral surface modification, catalysts and many other fields, with very high application prospect and strategic value.
There aret wo ways to extract lithium from ores such as spodumene and lapidolite. In recent years, with the progress of science and technology, more and more diversified application chains have been derived from lithium chemical products such as lithium carbonate and lithium hydroxide, forming a strong down stream demand. On the one hand, the development of hybrid and pure electric vehicles has led the explosive demand for battery-grade lithium carbonate and battery-grade lithium hydroxide in the world. On the other hand, the demand for lithium batteries from digital 3C products is still strong. Ceramic and other traditional areas are long-term stable. On the whole, the demand for lithium will maintain a strong growth trend. Its price will rise from around 40,000 yuan before 2015 to 120,000 yuan by the end of 2015, reaching a maximum of 170,000 yuan in the first half of 2016. According to the long-term planning of new energy vehicles released by various countries, lithium carbonate and lithium hydroxide, which are important materials for power batteries, bring huge market opportunities and broad prospects for development.
According to the forecast of Roskill, which is an industry data service provider, the world wide demand for lithium would reach over 1 million tons by 2026, with a compound annual growth rate of 18%. The major drivers come from the battery industry, especially the new energy automotive batteries. In 2017, China produced 83,300 tons of lithium carbonate, 39,900 tons of lithium hydroxide, 16,000 tons of lithium chloride, with a total of 135,000 tons of lithium salt (convert into lithium carbonate equivalent), increasing 44.3% over the same period of last year. The total output of cathode materials exceeded 300,000 tons. The current total capacity of lithium salt in China has reached 200,000 tons. Despite all the parties make efforts to increase their production capacity, a large number of lithium salt supply shortfalls are still expected to occur each year by 2025, taking into account of the distribution and development of lithium resources, the design, construction and operation of lithium salt production lines.
After years of scientific research and technology development, Hubei University Tianshu Industrial Research and Design Instituteof New Energy Materials and Hubei University have achieved a series of major breakthroughs in extracting lithium from spodumene and lapidolite, through the lithium-based material spreparation technology and equipment with independent intellectual property rights.
On the basis of studying the crystalline mineralogy of silicate science and natural minerals, our institute takes the microstructure as the main research method, combining with crystallography and related disciplines, through the Key Laboratory of the Ministry of Educationand Key Laboratory of Hubei Province to carry out in-depth study of lithium-base material microstructure. The structure determines properties, various characteristics of lithium salt materials such as (sub) grain boundaries, defects, crystal orientations, grain boundaries and porosities, can be analyzed from the microstructure.We analysis and study the structural of raw materials and products, find out the correlation between the microstructural change characteristics, different temperatures and atmospheres in the production process, so as to determine the reasons for material property changes due to external conditions and internal structure, and improve the production process and product quality, reduce raw material consumption, etc. We have mastered the crystal structure change principle of spodumene/lapidolite, and lithium extraction technology.
In the field of lithium battery materials, our institute covers from the cathode materials (lithium cobalt oxide, lithium nickelate, lithium cobalt nickel manganese, lithium iron phosphate and ternary materials, etc.), negative electrode materials (graphite and lithium titanate), electrolyte, diaphragm, aluminum shell, and related products, etc., including the upper, middle and lower reaches the lithium-based materials industry chain.
In the practice of industrialized production, through the optimization and innovation of the original production line and equipment, we have realized the crystal form conversion by the differential thermal calcination mode in the spodumene / lapidolite extraction technology, as well as the acidification roasting, leaching (filtration), freezing crystallization and a series of major key technologies. We creatively research and develop new technologies, processes and equipment with independent intellectual property rights. Applying the new spodumene differential thermal roasting crystal transformation process, the key technology and equipment of spodumene preheating energy storage and conversion, short flame differential thermal high radiation burner, the key technology and equipment of crystal stable and cooling of β-spodumene, ceramic atomization with high mixing acidity, crystallization cooling and stirring treatment technology and equipment, acid mist treatment technologies and equipment, dynamic online dryer, particle size separator, anti-bonding hoist, uniform radiation acidification kiln, high heat transfer rate cooling kiln and other production processes.
It is applied in the chemical section, the liquid is delivered to irrigation system intight pipeline without waste water discharge. The important media such as slurry irrigation and freezing irrigation are made of stainless steel. The advanced MVR evaporation and concentration technology can reduce the energy consumption of the system. The efficient freezing unit improves the crystallization efficiency, we can save the construction investment by combination of optimization ofthe lithium carbonate and lithium hydroxide production process, differential heating proprietary technology and special equipment to significantly improve the conversion rate and acidification rate of spodumene, the new filtration equipment and leaching residue washing method to reduce thelithium lossinslag, advanced technology and energy-saving measures to significantly reduce lithium loss in sodium sulfate decahydrate and anhydrous sodium sulfate lithium. Our new technology achieves saving 80% of CO2 usage.
We have signed many engineering design contracts covering transformation and acidification sectionsin production of battery grade lithium carbonate andlithium hydroxide, such as Baijierui Advanced Materials Corporation (Jingmen). The cumulative total amount of battery grade lithium carbonate has reached 60,000 tons, and 50,000 tons of battery grade lithium hydroxide.
II. Innovations in Lithium-based Material Preparation Technology
1) Applying online dryer,we can make full use of the kiln exhaust gas to dry materials, with high thermal efficiency, reduce system heat consumption.
2) The dry material delivered into the preheater can reduce the load on the preheater, reducethe preheater diameter, increase the temperature feeding into the kiln,with small crystal transition temperature difference and high rate of crystal transformation.
3) The dry material delivered into the preheater can reduce the evaporation of water vapor, thereby reducethe air quantity of the exhaust fan,with smaller fan power ,which saves power consumption.
4) The drying material delivered into the preheater and rotary kiln forroasting, with stable material ingredient, which guarantees the stable product quality after roasting, and the operation iseasy to control.
5) Applying the specialized powder separator independently research and development by our institute, according to the physical and chemical properties of the materials, we have designed decentralized, grading and separating stage, to achieve scientific and reasonable particle size cutting, so that the material particlesget more uniform distribution, with narrower particle size distribution.
6) High temperature and high humidity dust treatment have overcome the traditional bag filter just only deal with the dry materials, the treatment of the wet dust with 15% moisture to achieve a good separation of materials and gas, the moisture of products is less than 0.5%, with large handling capacity of wet dust per unit time, no congestion and no condensation.
7) Applying German Pfister measurement for measuring the raw material, with accuracy measurement, andsmall error, only ± 0.5%, can reduce the instability caused by fluctuations in raw materials, energy conservation.
8) Applying the specialized grate coolerfor cooling ofthe conversion materials,with good cooling effect, low crystal transformation temperature,and the waste heat can be fully recycled.
9) The specialized internal structure of the mill has overcome material flow control, material lifting, gas flow, grinding output and increase the grinding efficiency of the mechanical energy problems in the ball mill, the optimization of particle morphology, which enhances the grinding ability.
10) Applying bag filters at all the dust points for dust collection, the emission concentration can meet environmental requirements, with clean production environment.
III. Technical IndexesComparisonof OurNew ProcessProduction Line andTraditionalOnes.
|
Traditional |
New Process |
Conversion kiln energy consumption(kCal/kg) |
900~1200 |
650~680 |
Acidification kiln energy consumption(kCal/kg) |
160 |
130 |
Transformation rate(%) |
90 |
99 |
Acidificationrate(%) |
95 |
99 |
Process power consumption(kw.h) |
130 |
112 |
Total metal lithium recovery (%) |
70~80 |
90 |
lithium oxide contentin lithium slag |
≤0.3~0.45% |
≤0.25% |
lithium oxide contentinsodium sulphate |
≤0.2% |
≤0.1% |
Related Links:
Science and Technology Department of Hubei Province
http://www.hbstd.gov.cn/sjb/kjyw/tzgg/67728.htm